Grades
Titanium Grade 2
Description
Titanium Grades 1, 2, 3 and 4 are commercially pure (99% minimum titanium). Each grade has slight variations in chemical composition that affect mechanical properties and design capability. The corrosion resistance is similar across all four grades. Titanium is light weight, exceptionally corrosion resistant and often exceeds the corrosion resistance of stainless steels in most environments. Of the four commercially pure (C.P.) titanium grades, Grade 2 is the alloy of choice for most industrial applications that require good ductility and corrosion resistance.
Industries & Applications
Titanium Grade 2 has a lower density making it very desirable where weight can be a concern. Medical and aerospace are two key industries for titanium alloys. The strength and corrosion resistance properties of titanium Grade 2 also make it well suited to applications in the marine, chemical processing and desalination industries. Typical applications for Grade 2 titanium include oil & gas components, reaction and pressure vessels, tubing or piping systems, heat exchangers, liners, flue-gas desulphurization systems and many other industrial components. Continuous service temperatures can reach up to 800°F with occasional, intermittent service at 1000°F.
Resistance to Corrosion
Titanium’s C.P. grades corrosion resistance comes from a strongly adherent, stable, protective oxide film, which forms in the presence of oxygen. This film makes the commercially pure titanium grades resistant to most oxidizing, neutral and inhibited reducing, as well as mildly reducing environments. Grade 2 offers excellent resistance to seawater and marine atmospheric corrosion. Corrosion resistance is similar between the four C.P. grades, but mechanical properties vary along with varying oxygen and iron contents. Grade 2 titanium is resistant to attack from moist chlorides and metallic chlorides, chlorite and hypochlorite solutions, nitric and chromic acids, organic acids as well as many gaseous industrial applications.
Fabrication and Heat Treatment
Titanium Grade 2 has good ductility, which allows for cold formability. To prevent cold forming concerns, the minimum bend radius for material under 0.070″ thick should be 2T, while 2.5T should be used for material over 0.070″. The material can also be easily machined, hot worked and welded. Hot working should be performed between 400°F and 600°F. Stress relieving should be performed by heating to a temperature between 900°F and 1100°F followed by either forced air or slow cooling. Annealing temperatures range from 1200°F to 1400°F for 6 minutes to 2 hours followed by an air cool.
Welding of Grade 2 titanium can be performed using various methods such as MIG and TIG. Inert gas shielding is crucial to prevent oxygen pickup and embrittlement of the weld area. A mixture of argon and helium is typically preferred but should be tested prior to accepting a welding procedure. Preheat or post heat treatments are not required.
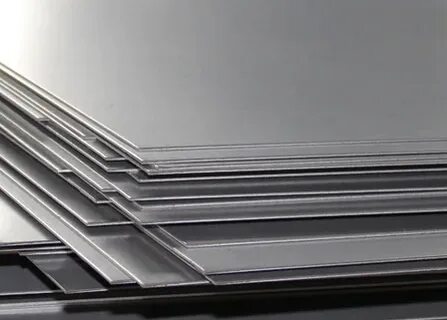
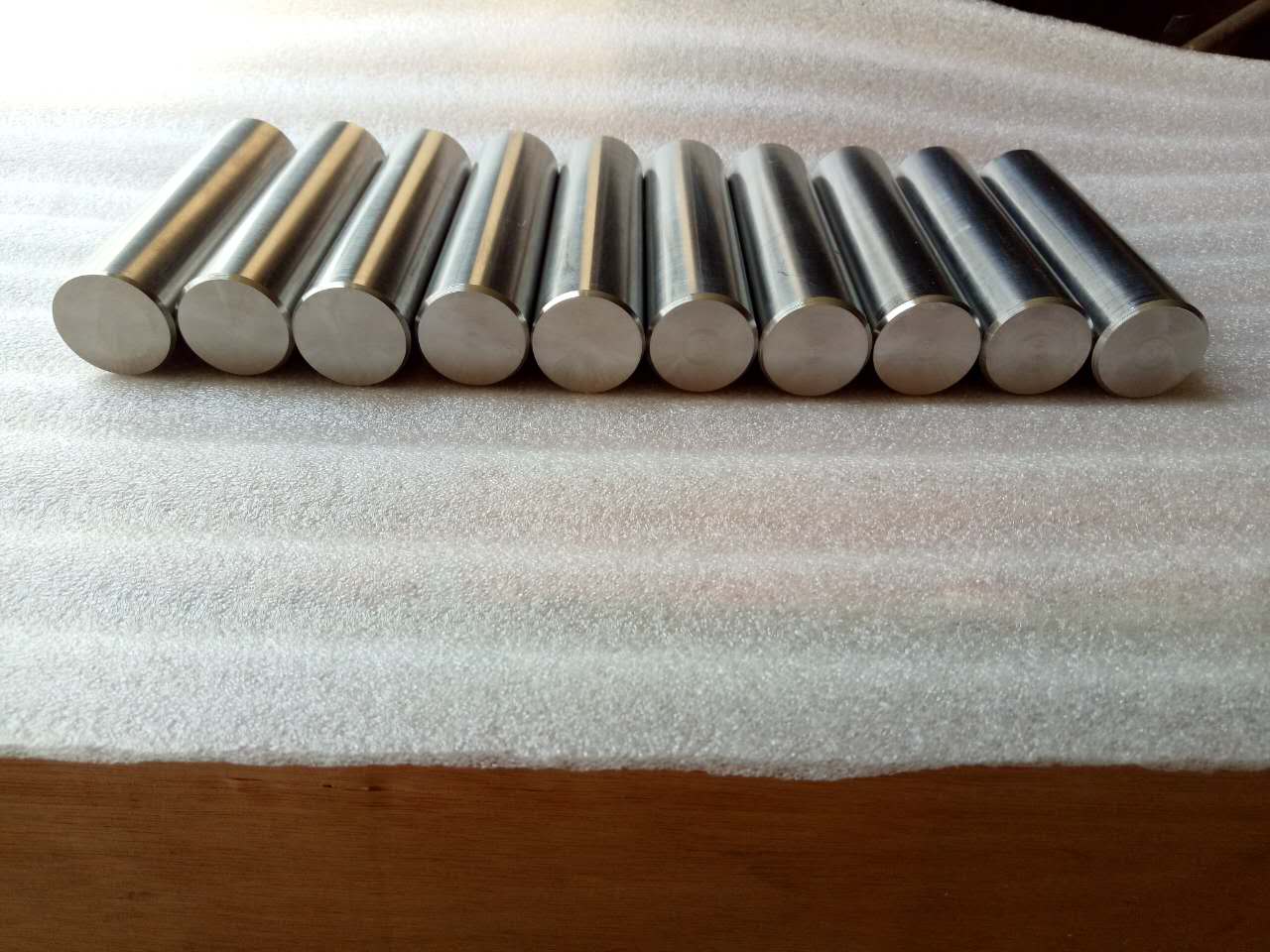
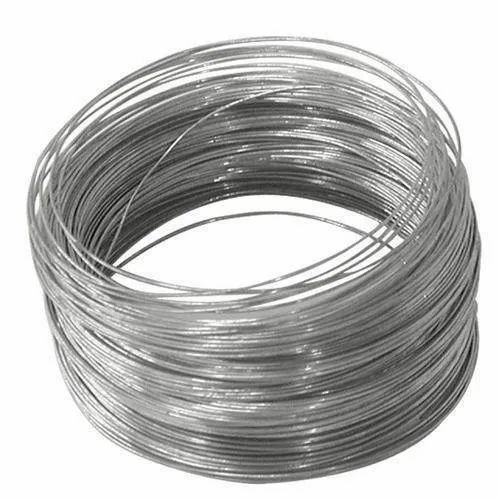
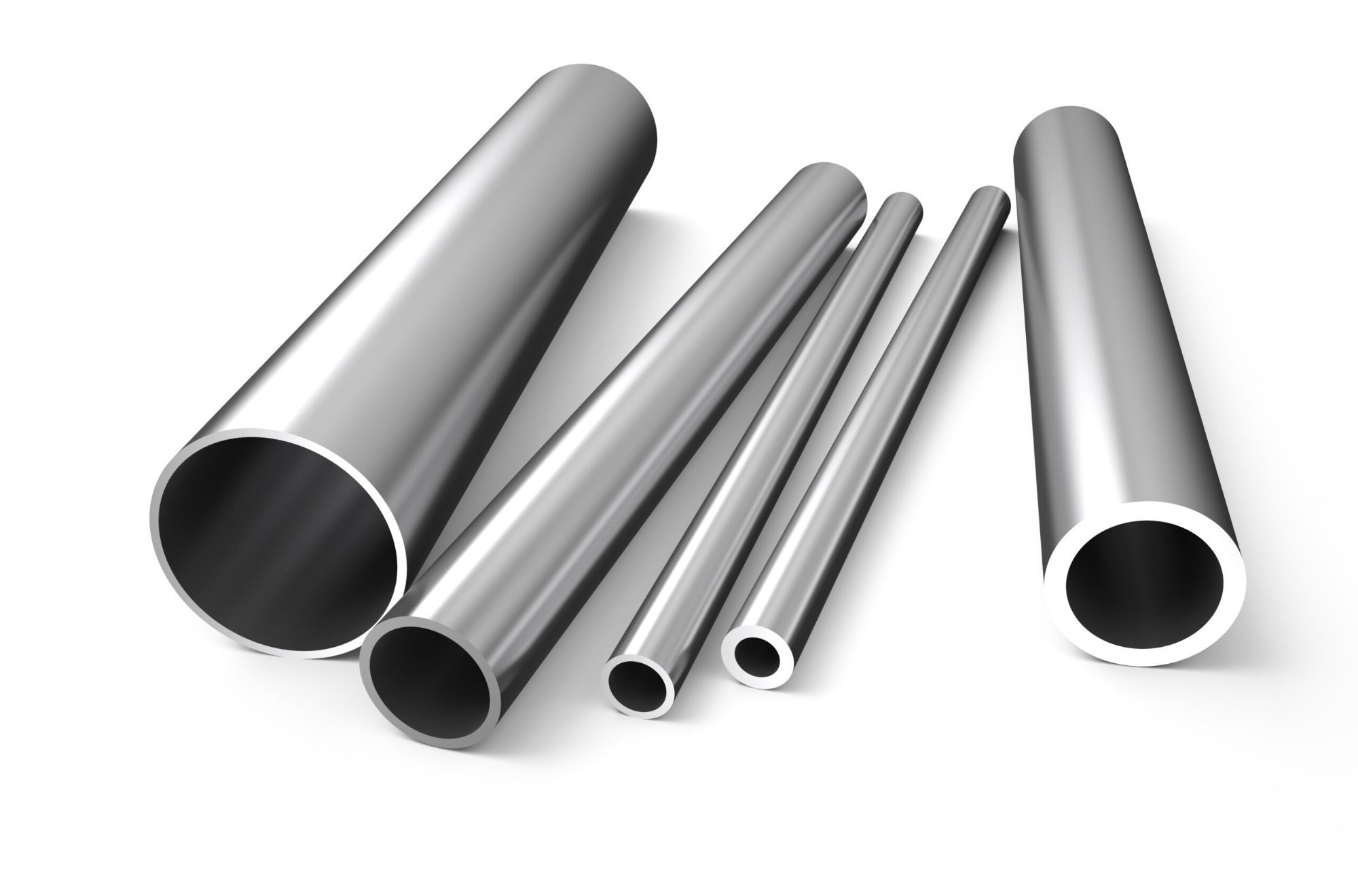
Titanium Grade 2, often referred to as “Commercially Pure” or “CP” Grade 2 titanium, is a popular and widely used grade of titanium metal. It is known for its excellent corrosion resistance, high strength-to-weight ratio, and biocompatibility. Here are some key characteristics and applications of Titanium Grade 2:
Corrosion Resistance: Titanium Grade 2 is highly resistant to corrosion, making it an ideal material for applications in aggressive environments, such as chemical processing, marine, and aerospace industries.
Strength: While not as strong as some other titanium alloys, Grade 2 titanium offers a good balance of strength and weight. It is stronger than most stainless steels while being significantly lighter.
Biocompatibility: Titanium Grade 2 is widely used in the medical field for implants, as it is biocompatible and non-reactive within the human body. This makes it suitable for bone plates, screws, and dental implants.
Weldability: Grade 2 titanium is easily weldable, making it suitable for various manufacturing processes and applications.
Low Density: Titanium has a low density, which means it is lightweight. This is particularly valuable in industries where weight savings are crucial, such as aerospace.
Heat Resistance: Titanium Grade 2 can withstand high temperatures, which makes it suitable for applications in the chemical and petrochemical industries.
Cost-Efficiency: Compared to some other titanium grades, Grade 2 is more cost-effective due to its lower alloying content.
Applications of Titanium Grade 2 include:
Aerospace: Used in aircraft components, such as airframes, engine components, and landing gear.
Chemical Processing: Suitable for equipment that comes into contact with corrosive chemicals.
Medical: Commonly used in surgical implants and medical devices due to its biocompatibility.
Marine: Used in boat components and offshore structures due to its resistance to seawater corrosion.
Power Generation: Used in power plant equipment like heat exchangers and condenser tubing.
Automotive: In some high-performance cars, Grade 2 titanium is used for exhaust systems and suspension components.
Sports Equipment: Some high-end sports equipment, such as bicycle frames and golf club heads, are made from Grade 2 titanium due to its strength and lightweight properties.
Overall, Titanium Grade 2 is a versatile material with a wide range of applications, where its combination of properties makes it highly desirable in various industries.
Products and Size Ranges
We supply hardness of wire (Soft, Quater Hard, Half Hard) according to customer requirements.
Material Certification and Traceability
At Satyam Overseas, we prioritize Material Certification and Traceability. Our materials, meeting ASTM and ASME standards, come with 3.1 Mill Test Certificates as a guarantee of compliance. Additionally, upon request, we provide 3.2 Mill Test Certificates for added assurance. Every material is clearly marked and accompanied by a corresponding certificate, meticulously linking markings to certification. This meticulous approach ensures complete accountability and unwavering reliability throughout our supply chain.
Chemical Composition
O | N | C | H | Fe | Al | V | Ni | Mo | Others | Residuals |
---|---|---|---|---|---|---|---|---|---|---|
0.20 | 0.05 | 0.08 | 0.015 | 0.40 | 5.5-6.75 | 3.5-4.5 | 0.4 |
Physical properties
Melting point, ± 15 °C | 1650 °C |
---|---|
Density | 4.43 g/cm3 |
Beta transus, ± 15 °C | 995 °C |
Thermal expansion, 20 – 100 °C | 9.0 *10-6 K-1 |
Thermal expansion, 0 – 300 °C | 9.5 *10-6 K-1 |
Thermal conductivity, room temperature | 6.6 W/mK |
Thermal conductivity, 400 °C | 13 W/mK |
Specific heat, room temperature | 0.57 J/gK |
Specific heat, 400 °C | 0.65 J/gK |
Electrical resistivity, room temperature | 171 µW*cm |
Poisson’s ratio | 0.30-0.33 |
Physical properties
Forms | ASTM | ASME | DIN |
---|---|---|---|
Sheet and plate | B265 | – | – |
Bars and billets | B348 | – | – |
Castings | – | – | B367 |